Contents
Underground mining is one of two dominant mining techniques that are used for mineral exploration. It involves creating tunnels and shafts underground and extracting ore deposits from here. This article delves into the benefits and challenges of underground mining, while also offering an outlook on the technological advances made in this mining method.
What is underground mining?
Underground mining involves extracting ore from beneath the Earth’s surface by creating networks of tunnels and shafts that access mineral-rich zones deep underground. Unlike open-pit mining, which removes ore by excavating large surface craters, underground methods are chosen when the deposit is located too deep for surface mining to be economical – or when surface disturbance must be minimized.
Despite its relatively smaller surface footprint, underground mining is highly complex, requiring careful engineering to ensure safety, ventilation, and ore recovery under intense geological pressures. Though more expensive and labor-intensive than open-pit mining, it remains essential for accessing high-value orebodies across the globe.
Outlook on underground mining
As global demand accelerates for minerals essential to renewable energy technologies, electronics, and modern infrastructure – such as nickel, cobalt, rare earth elements, and gold – mining companies are increasingly turning to underground methods. Many of these critical minerals are found in deeper, more geologically complex orebodies that are often located in remote or environmentally sensitive areas. In such cases, open-pit mining becomes impractical or socially unacceptable, making underground mining a crucial way of unlocking these strategic resources.
Why do underground mining over other mining possibilities?
A deposit is considered for underground mining when the orebody is deep, narrow, or located beneath sensitive land areas such as urban zones, protected ecosystems, or major infrastructure.
Depth and geometry of the deposit
- Deep ore zones: Deep, high-grade ore zones that would require excessive waste stripping in an open-pit setting are ideal.
- Narrow ore bodies: Narrow veins or steeply dipping ore bodies are often more efficiently mined underground.
Surface constraints
When land access is limited – due to ownership, regulations, or ecological sensitivity – underground mining minimizes surface disruption.
Ore value
High-grade ores justify the higher cost of underground extraction, especially when the mineral content is dense and concentrated.
Emerging technologies in underground mining
The future of underground mining is being shaped by a number of transformative trends. Automation and robotics are at the forefront, with the adoption of driverless trucks, autonomous drilling rigs, and remote-controlled loaders significantly improving safety conditions while reducing the reliance on human labor in hazardous zones. These innovations are particularly important in the pursuit of critical minerals, where efficiency and precision can determine economic viability.
AI trends
Equally important to automation is the integration of real-time monitoring and artificial intelligence (AI). Underground operations are increasingly equipped with sensor networks that continuously track structural stability, air quality, water inflows, and equipment performance. AI systems analyze this data in real-time, enabling operators to optimize workflows, anticipate failures, and minimize disruptions. This data-driven approach is particularly valuable in complex underground environments where access to critical minerals must be both safe and selective.
All-electric mining
The move toward all-electric mines is another significant development. As part of broader efforts to decarbonize operations, companies are replacing diesel-powered machinery with electric alternatives and integrating renewable energy sources wherever possible. These low-emission systems not only reduce ventilation requirements but also align with rising environmental, social, and governance (ESG) standards – standards that are increasingly decisive in determining whether a critical minerals project secures its social license to operate.
ESG considerations
ESG considerations now play a central role in the approval and long-term success of underground mining ventures. Projects must demonstrate sensitivity to community concerns, cultural heritage, and groundwater systems. Transparent stakeholder engagement and inclusive planning are no longer optional – they are essential prerequisites for gaining trust and ensuring continued access to high-value deposits.
In summary, while underground mining involves greater technical complexity and financial commitment, it offers a vital route to accessing the critical minerals that are needed in the global energy transition and digital economy. Its future will depend not only on engineering ingenuity but also on how responsibly and sustainably companies navigate the challenges of working beneath the Earth’s surface.
Benefits to doing underground mining
Lower surface impact
- Minimal landscape alteration: Because much of the infrastructure is below ground, the visual and ecological footprint is far smaller than in open-pit operations.
- Preservation of surface land use: Useful in agricultural or urbanized areas where continued surface activity is desirable.
Access to deep deposits
- Feasible at great depths: Underground methods can extract ore located hundreds or even thousands of meters below ground level – far deeper than practical open-pit limits.
Selectivity and precision
- Targeted extraction: Precision drilling and blasting allow for the careful extraction of ore, minimizing dilution from surrounding rock.
- Reduced waste rock volume: As only the ore is typically removed, less waste needs to be managed.
Long-term production potential
- Expandable networks: Underground tunnels and stopes can be extended incrementally, making underground mines adaptable to changing geological understanding and commodity prices.
Limitations and possible challenges
While underground mining can be more sustainable on the surface, it brings unique operational and environmental challenges.
Safety risks
- Cave-ins and ground failure: Structural integrity of tunnels must be constantly managed to prevent collapses.
- Air quality: Poor ventilation can lead to buildup of toxic gases (e.g., methane, carbon monoxide), requiring continuous airflow systems.
- Seismic activity: In deep or geologically active zones, mining can trigger or be affected by underground tremors.
High costs
- Capital-intensive: Shaft sinking, ventilation, dewatering systems, and safety infrastructure add significant upfront and ongoing costs.
- Labor demands: Requires more personnel per tonne of ore compared to open-pit mining.
Limited ore recovery
- Access constraints: Not all ore can be safely or economically reached, especially near support pillars or weak rock zones.
- Dilution risks: In complex deposits, unintended mixing with surrounding rock can reduce ore quality.
Water and heat management
- Flooding risk: Groundwater ingress is common and requires constant pumping.
- Heat stress: Deeper mines often exceed 40°C, necessitating powerful cooling systems for human operation.
Surface subsidence
- Ground movement: Over time, underground voids may collapse, causing land above to sink or crack – especially problematic in populated areas.
A historical perspective on underground mining
Underground mining techniques date back thousands of years. Early miners in Egypt, Greece, and Rome used primitive hand tools to follow ore veins underground, with firesetting as one of the earliest forms of hard rock mining. Firesetting involved heating rock then quenching it with water to crack it. The labor was hard and dangerous, yet it allowed access to richer, more concentrated ores than those available at the surface.
In the Middle Ages, miners developed vertical shafts and timbered tunnels to reach deeper deposits. Water-powered hoists and ventilation shafts improved productivity and safety. By the Industrial Revolution, gunpowder and later dynamite allowed deeper and faster excavation. Steam engines replaced human and animal power for hauling ore and draining water.
In the 20th century, technological advancements such as mechanized drilling, rock bolting, and electric locomotives transformed underground operations. Today, modern underground mines often resemble small cities, complete with electrified haulage systems, automated loaders, and sophisticated monitoring systems. Digital mapping, automated drilling rigs, and tele-remote operations have become standard features, enhancing both safety and efficiency.
Take advantage of our advanced borehole steering technology
Aziwell is a leading provider of directional drilling solutions and offers service, rental, and software products for directional drilling. At the heart of this is our advanced borehole steering technology, which reduces environmental footprint through fewer drill pads, operational time and CO₂ emissions. Our borehole steering is precise, does not require special rods or rigs, and has no depth limitations.
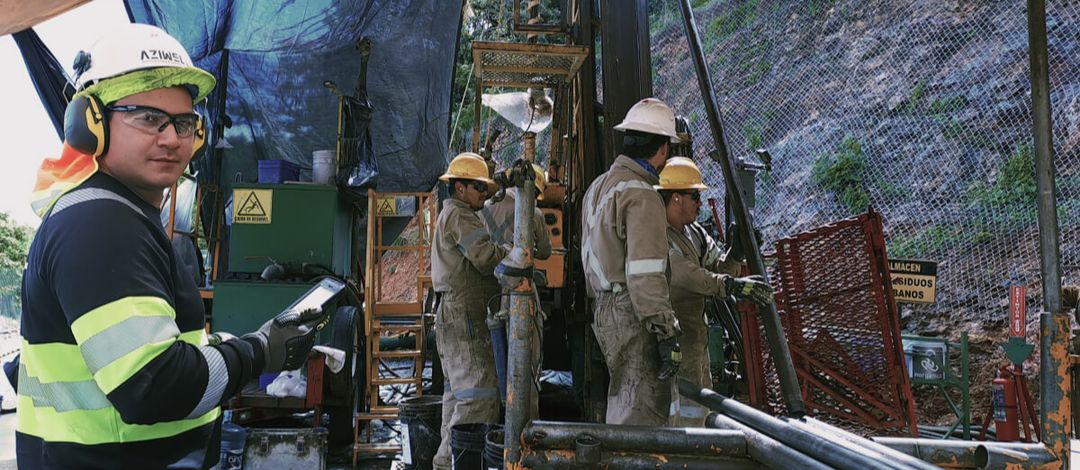